Polymer Testing Newsletters
Back to newsletters
Fleming PTC has added a laser die swell system to its Malvern Instruments Rosand RH7 twin bore capillary rheometer.  The system allows the accurate and continuous measurement of polymer die swell, which is an important rheological measurement, instrumental in the understanding of elasticity.  Elasticity is important in polymer extrusion, since most polymers in the melt phase are viscoelastic.  Such materials will swell to some degree on exiting a production die a problem if you want your extrusion to share the dimensions of your die!  Melted polymers, in most cases, experience stretching through extrusion dies, and due to the restoring forces generated, will try to return to their original state on exit (swelling).  The magnitude of the restoring forces defines the elasticity, which can be hard to measure in an absolute fashion (first normal stress difference, N1), however, die swell, is a convenient way to infer the elasticity the more the swell the more elastic the polymer.  In this way, screening of various grades can predict which are more elastic and which will swell more.  Once elasticity is inferred, a designer can work on either refining the die design and/or process conditions to achieve the desired degree of swell, or the grade could be switched altogether in favour of a more suitable alternative.  In either case, knowledge of this important rheological parameter allows choices to be made which may otherwise appear impossible.  The measurement is described in ISO11443:2005, 8.7 Determination of extrudate swelling.
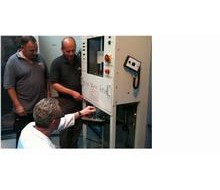
Fleming PTC has added a laser die swell system to its Malvern Instruments Rosand RH7 twin bore capillary rheometer. The system allows the accurate and continuous measurement of polymer die swell, which is an important rheological measurement, instrumental in the understanding of elasticity. Elasticity is important in polymer extrusion, since most polymers in the melt phase are viscoelastic. Such materials will swell to some degree on exiting a production die; a problem if you want your extrusion to share the dimensions of your die! Melted polymers, in most cases, experience stretching through extrusion dies, and due to the restoring forces generated, will try to return to their original state on exit (swelling). The magnitude of the restoring forces defines the elasticity, which can be hard to measure in an absolute fashion (first normal stress difference, N1), however, die swell, is a convenient way to infer the elasticity; the more the swell the more elastic the polymer. In this way, screening of various grades can predict which are more elastic and which will swell more. Once elasticity is inferred, a designer can work on either refining the die design and/or process conditions to achieve the desired degree of swell, or the grade could be switched altogether in favour of a more suitable alternative. In either case, knowledge of this important rheological parameter allows choices to be made which may otherwise appear impossible. The measurement is described in ISO11443:2005, 8.7 Determination of extrudate swelling.
Telephone:
01299 251 914
Our postal address:
Fleming
Polymer Testing Ltd,
Holly House
Hartlebury
Kidderminster
DY11 7TE UK